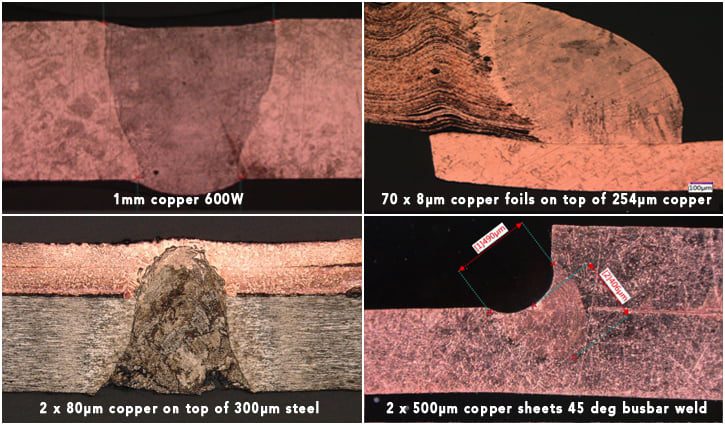
Blue Laser Welding
Welding is about more than just melting adjacent metals.Ā The factory floor demands the rapid reconfiguration and the flexible geometry possible with laser welding.Ā Traditional infrared lasers ā although powerful and flexible ā just arenāt suited for welding reflective metals.Ā Too much of their energy is wasted, ending up as voids and spatter, defects that can be fatal for both structural and electronic applications. The fundamental physics of the industrial blue laser, along with the high brightness of NUBURUās chip-based design, lead to unprecedented quality.Ā Perhaps even more importantly, this quality doesnāt come at the expense of speed.Ā Blue laser welding is both faster and higher quality than infrared laser welding.